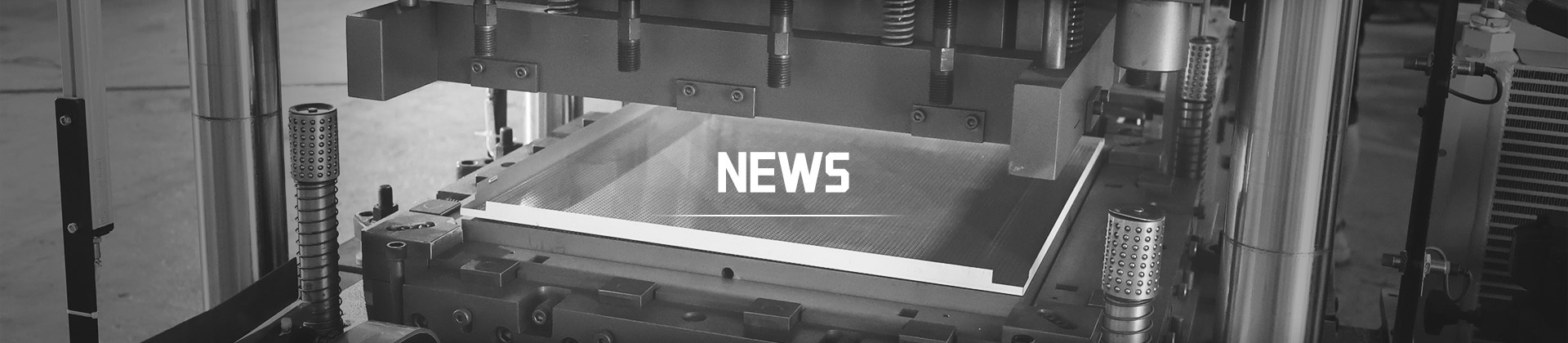
How to use metal sheet perforated machine?
2025-03-10 17:00
Definition of metal sheet perforation line
A metal sheet perforated machine is a device dedicated to processing metal sheets. By placing the metal sheet into the metal sheet perforation line and using the strong pressure of the punch, the metal perforated making machine can form holes of various shapes and sizes on the metal sheet to produce metal perforated sheets. This metal sheet perforated machine is widely used in many industries and is valued for its efficient production capacity and flexible processing options.
Uses of metal sheet perforation line
Metal perforated sheets are widely used in modern industry and construction. Here are some of the main uses:
1. Construction industry: Metal perforated sheets are often used in building facades, partitions, ceilings and other decorative materials. They not only have beautiful appearance, but also provide good ventilation and lighting effects.
2. Filtration and ventilation: In water treatment, air filtration and ventilation systems, perforated sheets are used as filters and vents, which can effectively control the flow of fluids.
3. Audio equipment: Perforated sheets are often used in the shell of audio equipment, which can effectively control the propagation of sound and reduce noise.
4. Traffic and Transportation: In automotive and aviation manufacturing, metal perforated sheets are used for lightweight design, which can reduce overall weight and improve fuel efficiency.
5. Household Goods: In furniture and home decoration, perforated sheets are used as partitions, guardrails and decorative panels, which increase the beauty and practicality of the products.
6. Electronic Equipment: In electronic products, perforated sheets are used for heat dissipation and protection, which can effectively improve the performance and service life of the equipment.
Ways of using metal perforated making machine
The process of using the metal perforated making machine is relatively simple, but certain steps need to be followed to ensure the efficiency and quality of the processing. The following are the basic methods of using the metal sheet perforation line:
Uncoiling
Before the processing begins, the metal coil needs to be placed on the decoiler of the metal sheet perforated machine. The uncoiling process includes the following steps:
- Placing the coil: Place the metal coil on the base of the decoiler to ensure that the coil is firmly fixed in place.
- Adjust the tension: According to the thickness and type of the coil, adjust the tension of the decoiler to ensure that the coil will not be twisted or deformed during subsequent processing.
- Determine the material width: According to the specifications of the metal perforated making machine, ensure that the width of the metal coil is suitable for the subsequent leveling and punching operations.
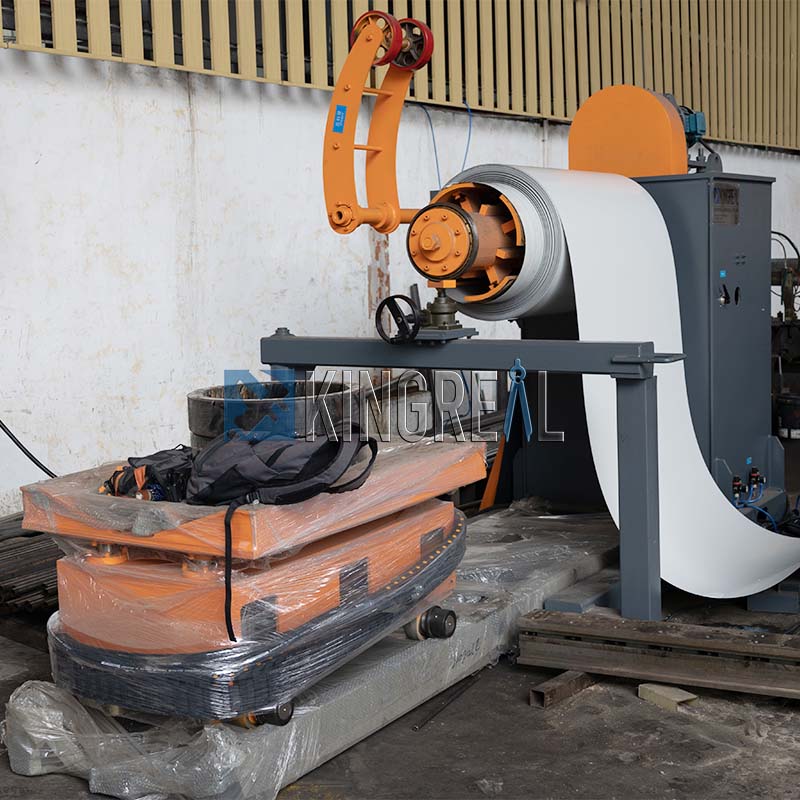
Leveling
The metal coil after unwinding usually has a certain bend or wave shape, which needs to be leveled by the leveling machine. The purpose of leveling is to ensure that the metal sheet can withstand pressure evenly during the punching process and avoid unnecessary deformation. The leveling process includes:
- Feeding: Feed the metal sheet into the leveling machine to ensure that it fully enters the leveling area.
- Adjust the leveling machine: According to the thickness of the metal sheet and the type of material, adjust the pressure and gap of the leveling machine to achieve the best leveling effect.
- Check the flatness: After the leveling is completed, check the flatness of the metal sheet to ensure that there are no obvious waves or bends.
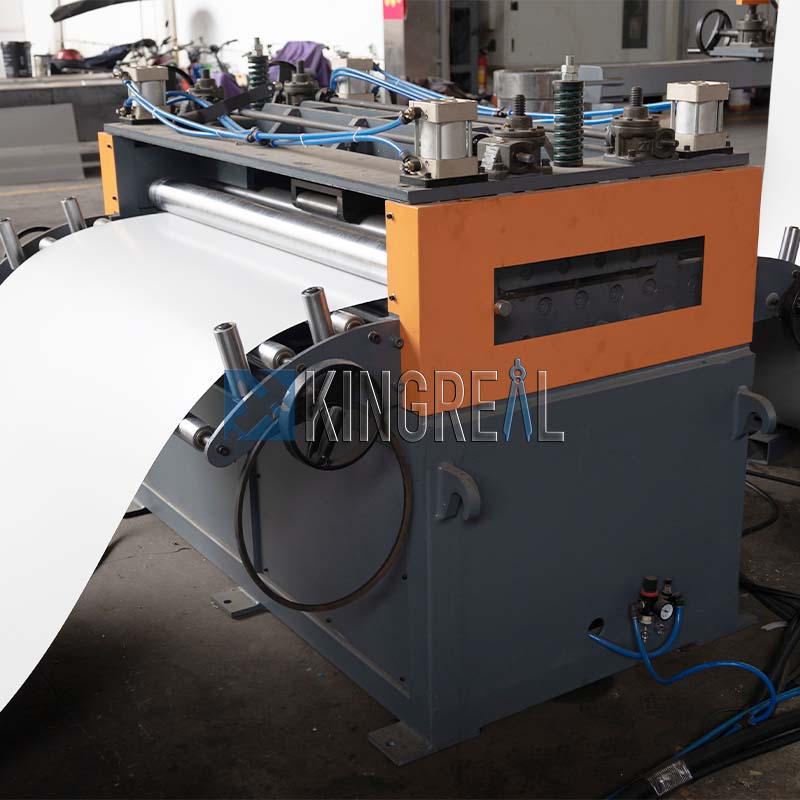
Punching
Punching is the core processing step of the metal sheet perforation line. In this stage, the metal sheet will pass through the metal perforated making machine and form the predetermined holes through the action of the punch. The specific steps are as follows:
- Set punching parameters: According to the design requirements, set the parameters of the metal sheet perforation line, including hole diameter, hole spacing and punching speed. The setting of these parameters directly affects the quality and efficiency of punching.
- Feeding: Feed the flattened metal sheet into the metal perforated making machine to ensure that it is in the correct position and aligned with the punching head.
- Start the metal sheet perforated machine: Start the metal sheet perforation line, and the punch will punch the metal sheet at the set speed and pressure. Pay attention to the punching process to ensure that no abnormalities occur.
- Monitor quality: During the punching process, regularly check the punching quality to ensure that the size and shape of each hole meet the design requirements.
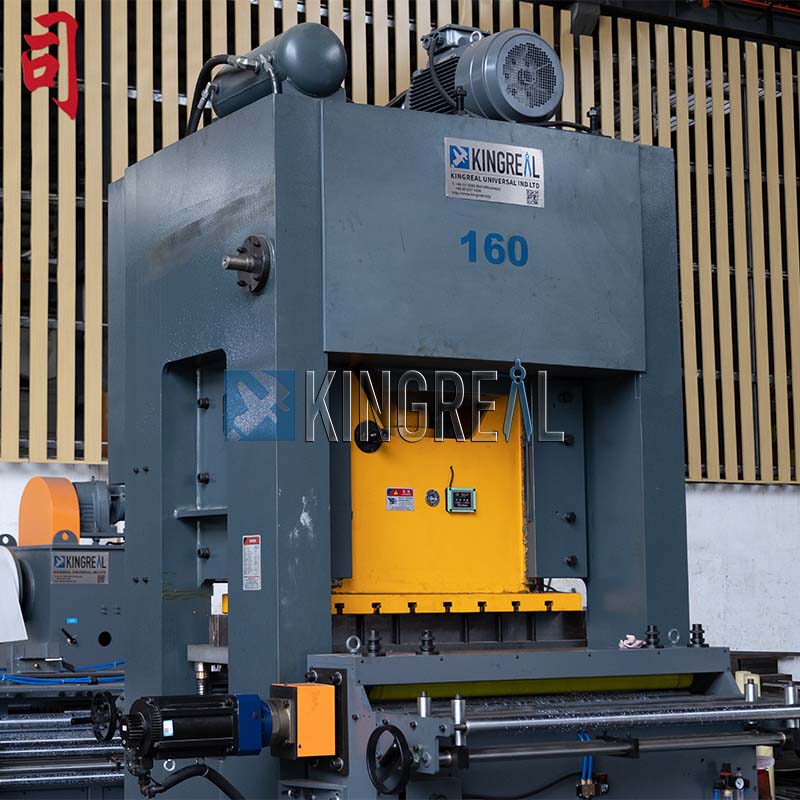
Cutting or Rewinding
After punching, the metal sheet can be cut or rewound as needed:
- Cutting: If the punched sheet needs to be cut into a specific size, a shear can be used for cutting. Ensure the position and size of the cut are accurate.
- Rewinding: If the punched sheet is long and does not need to be cut, you can choose to rewind it. The recoiler rolls the punched metal sheet into a roll for subsequent storage and transportation.
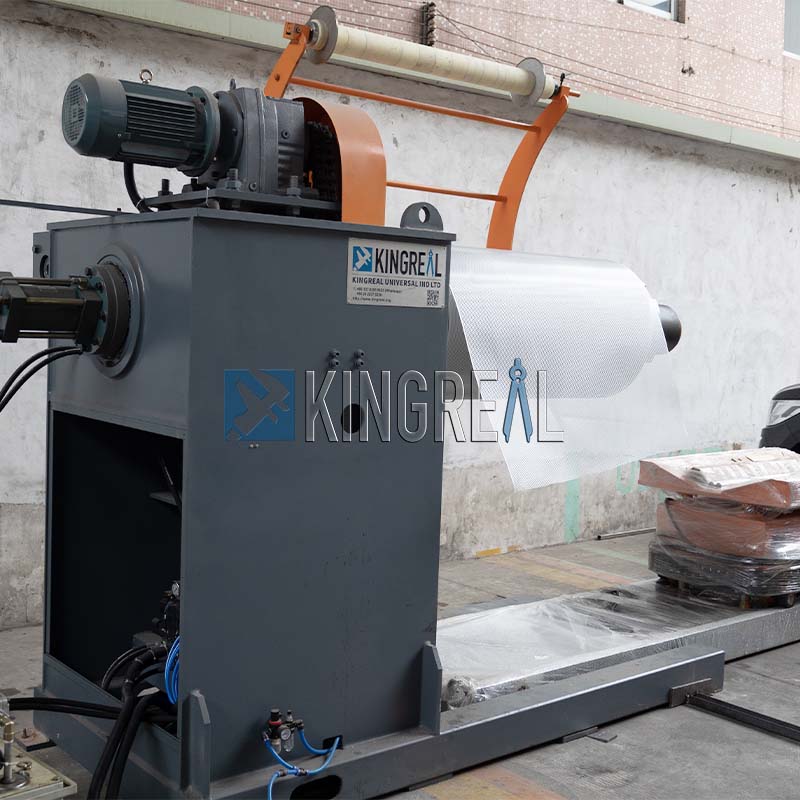
Precautions for using the metal perforated making machine
When using the metal sheet perforated machine, there are some important precautions to follow to ensure the safety of operation and processing quality:
1. Safe operation
- Wear personal protective equipment: When operating the metal perforated making machine, be sure to wear appropriate protective equipment, including safety glasses, gloves and earplugs, to ensure your own safety.
- Familiar with equipment operation: Before using the metal sheet perforation line, the operator needs to be familiar with the equipment's operating manual and understand the functions and safe operating procedures of each component.
- Ensure the normal operation of the equipment: Before starting production, check all parts of the equipment to ensure that there are no damaged or loose parts.
2. Material selection
- Select suitable metal materials: According to the punching requirements and application areas, select suitable metal materials such as stainless steel, aluminum alloy, etc. to ensure the strength and durability of the materials.
- Check the quality of materials: Before starting processing, check the quality of the metal coil to ensure that there are no obvious defects or damage to avoid affecting the punching quality.
3. Regular maintenance
- Regularly check the equipment: Regularly maintain and inspect the metal perforated making machine to ensure the normal operation of each component and replace damaged parts in time.
- Lubrication and maintenance: Regularly lubricate the equipment to reduce wear and extend the service life of the equipment.
4. Monitor the production process
- Real-time monitoring: During the punching process, the operator should maintain real-time monitoring of the production process to ensure the quality of punching.
- Adjust parameters in time: According to the actual production situation, adjust the parameters of the metal sheet perforation line in time to ensure production efficiency and product quality.
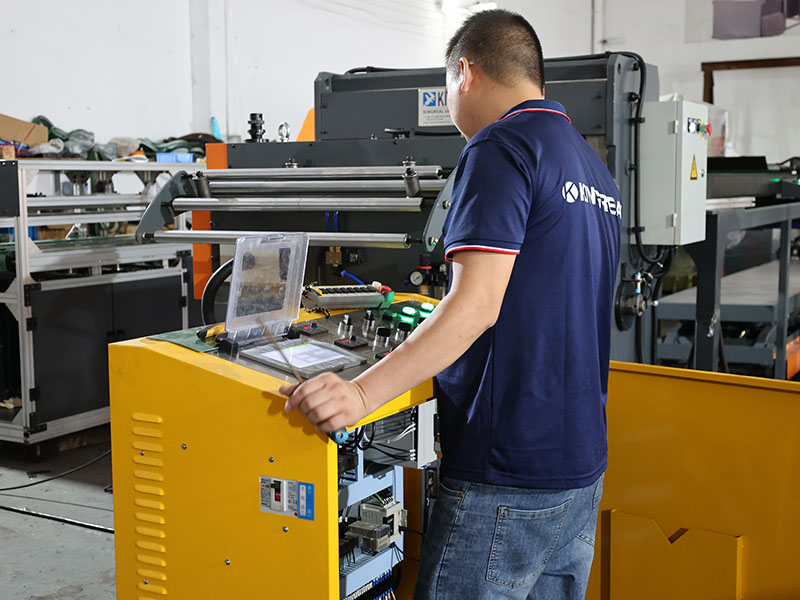
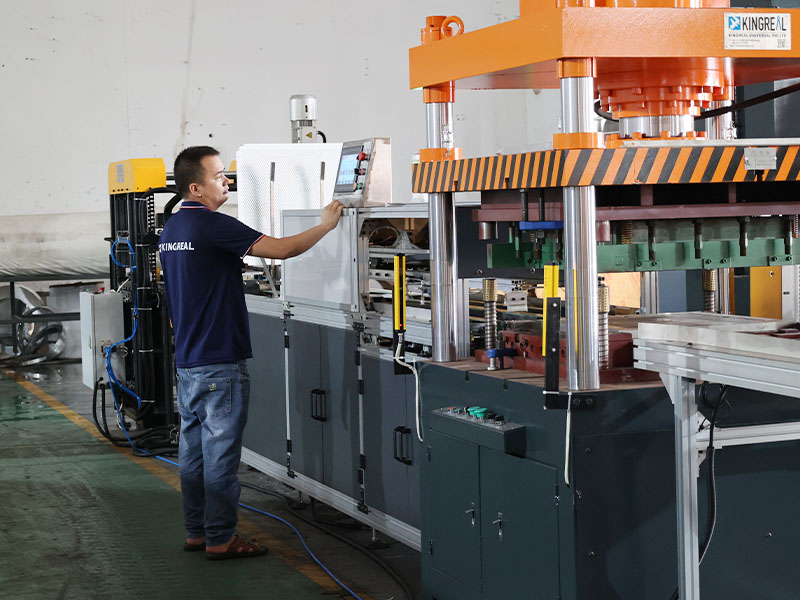
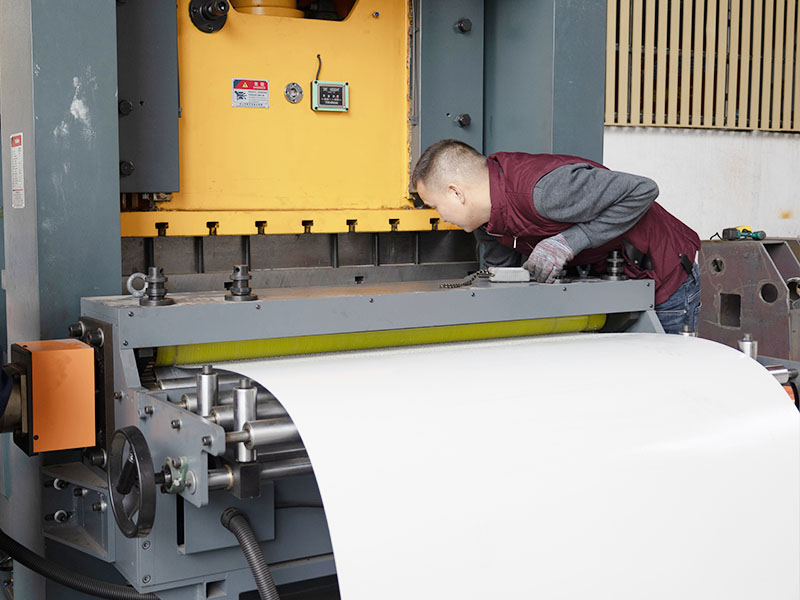
Get the latest price? We'll respond as soon as possible(within 12 hours)