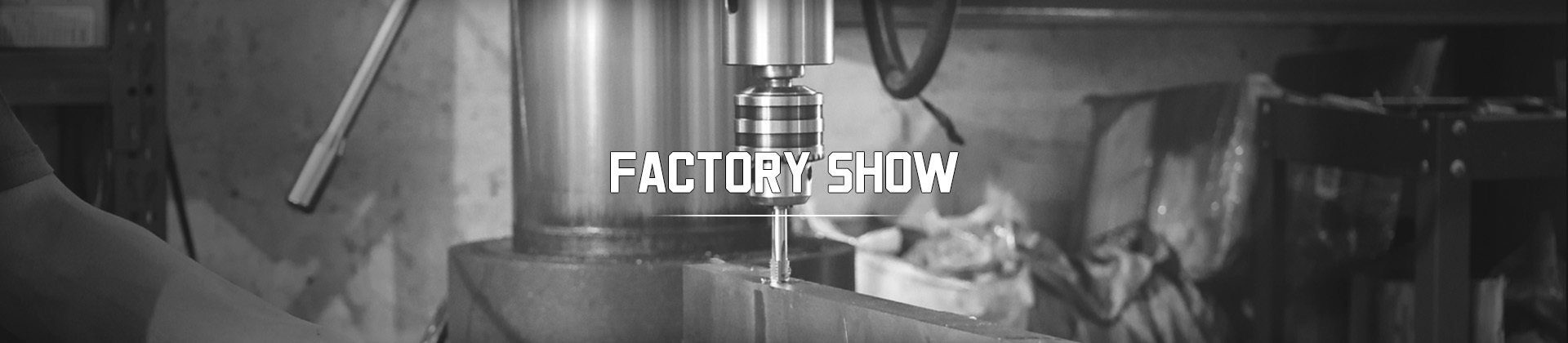
Processing Workshop
In the processing workshop of KINGREAL CEILING MACHINERY, the workers have rich experience in machine manufacturing and are familiar with the production process of customized machines. The team of KINGREAL CEILING MACHINERY not only has a solid technical background, but also continues to accumulate experience in actual operation to ensure that each machine can accurately meet the needs of customers. To this end, KINGREAL CEILING MACHINERY has set up processing workshops for different types of machines, which are mainly divided into suspended ceiling roll forming machine processing workshops and metal perforation line processing workshops.
Processing workshops for different machines
(1) Suspended ceiling roll forming machine processing workshop
In the suspended ceiling roll forming machine processing workshop, KINGREAL CEILING MACHINERY focuses on the production and manufacturing of a variety of equipment, including metal ceiling tile production lines, metal ceiling carrier machines, ceiling t bar machines. These equipment are an indispensable part of modern buildings. The Greek baffle ceiling machines, Vietnamese linear strip ceiling machines and Russian open cell ceiling machines recently shipped by KINGREAL CEILING MACHINERY have all been manufactured in this workshop.
Production Process
During the manufacturing process of the suspended ceiling machine, KINGREAL CEILING MACHINERY staff first produce various components, such as decoilers, precision straighteners, roll forming machines and cutting stations. Each component will undergo strict quality control during production to ensure that it meets the design standards. After processing, the staff will assemble these components to form a preliminary structure.
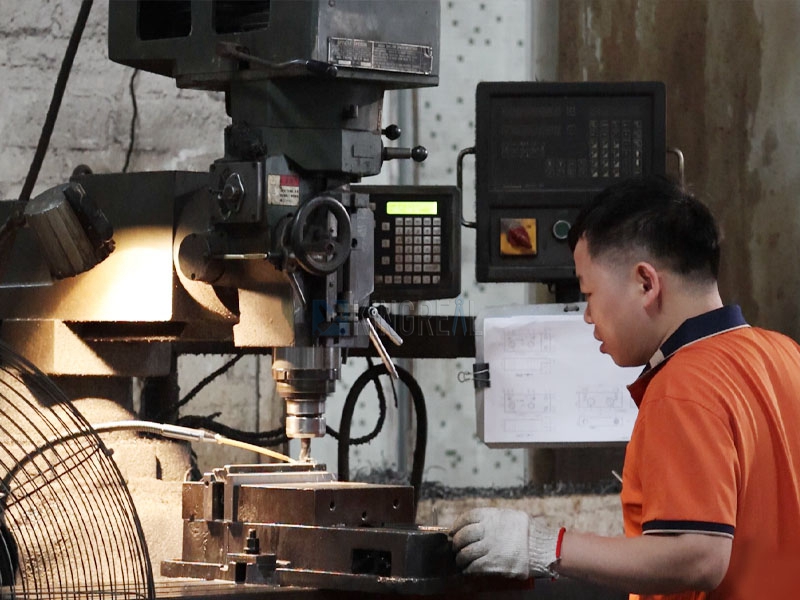
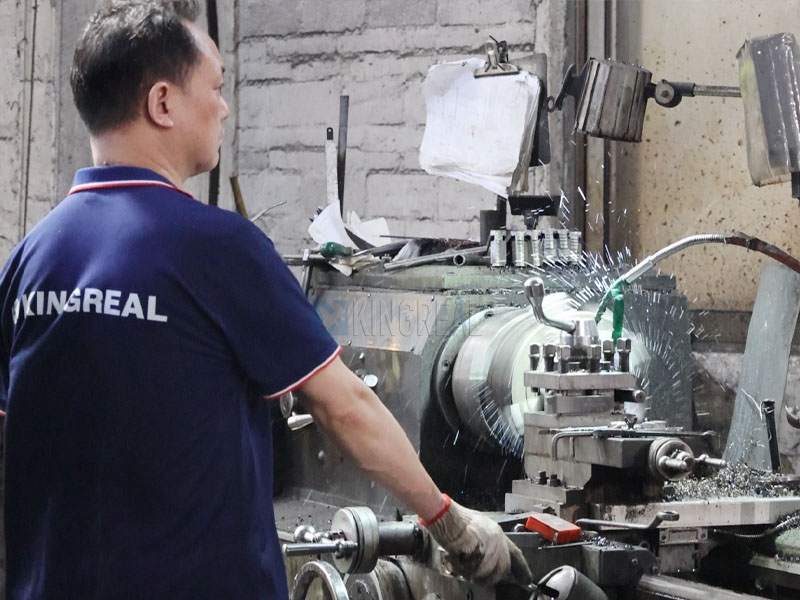
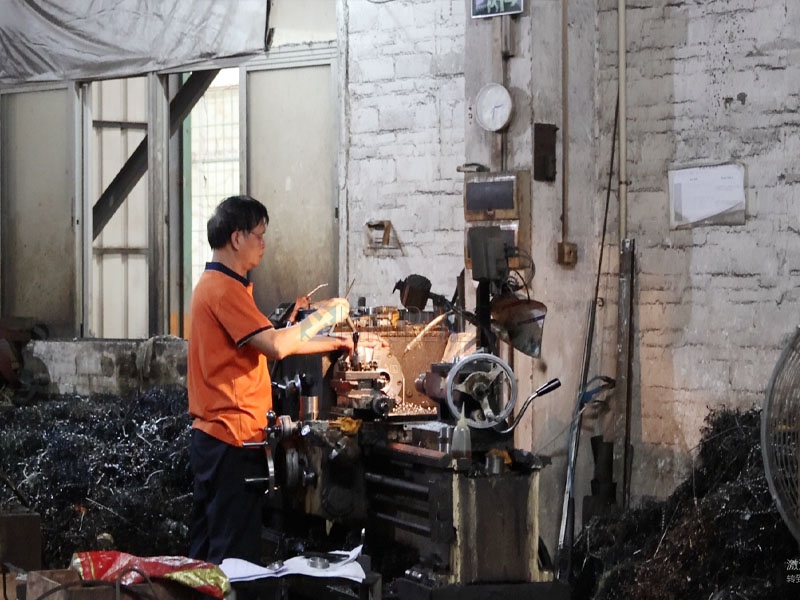
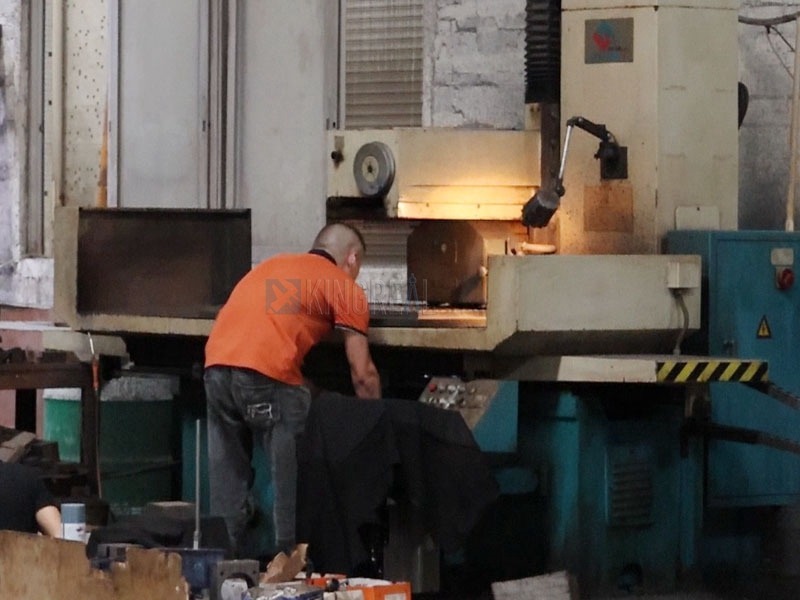
Production details
KINGREAL CEILING MACHINERY's precision straightener adopts a total of 21 rollers, with 10 rollers on the top and 11 rollers on the bottom, so that the material can better eliminate waves and bends when it is leveled.
The rollers of the main roll forming machine are made of high-strength CR12MoV material, which has excellent wear resistance and toughness. To further improve the performance of the rollers, KINGREAL CEILING MACHINERY uses a vacuum heat treatment process, supplemented by liquid nitrogen cooling, and undergoes three tempering treatments. This process ensures that the rollers are not easy to crack during long-term use, ensuring the stability of production and the high quality of the product.
The cutting station is a key component of the suspended ceiling machine, and its blades are also made of high-hardness materials to ensure its durability and shearing effect. The blades are finely ground to produce neat and smooth cuts, reducing the difficulty of subsequent processing. This design not only improves production efficiency, but also ensures the appearance quality of the final product.
Through the above detailed manufacturing process and strict quality control, KINGREAL CEILING MACHINERY ensures that each suspended ceiling machine can meet the high standards of customers and provide customers with reliable solutions.
(2) Perforated metal machine processing workshop:
In KINGREAL CEILING MACHINERY's metal perforated machine processing workshop, we have worked closely with customers from Bangladesh, Brazil and Greece to successfully manufacture a variety of equipment such as metal sheet perforation line, coil to coil perforation line. These machines not only meet customer needs, but also demonstrate KINGREAL CEILING MACHINERY's professional capabilities in the field of punching technology.
Production process of Punching die
1. Design stage:
- Engineers first use computer-aided design (CAD) software to carry out detailed design of the die. This stage includes comprehensive planning of punching shape, size and structure to ensure that it meets functional requirements and customer needs.
2. Material selection:
- It is crucial to choose the right material for the mold. KINGREAL CEILING MACHINERY usually uses high-strength steel or alloy materials, which have excellent wear resistance and service life and can withstand high-intensity punching operations.
3. Processing stage:
- Cutting: In the perforated metal machine processing workshop, the staff first cuts the mold material into the required shape and size according to the design drawings to ensure the accuracy of each component.
- Machining: Subsequently, the staff uses high-precision equipment such as milling machines, lathes and grinders for fine processing to ensure the accuracy and surface finish of the mold. This stage is the key to ensure the performance of the mold.
4. Heat treatment:
- After processing, the mold will be heat treated to improve the hardness and wear resistance of the material. This process can significantly extend the service life of the mold and ensure its stability in high-intensity work.
5. Assembly and surface treatment:
- Finally, the staff will assemble the cut and processed mold parts, including punches, die bases and guide columns. After assembly, the mold surface is coated as needed to improve corrosion resistance and reduce wear, thereby improving the overall performance of the mold.
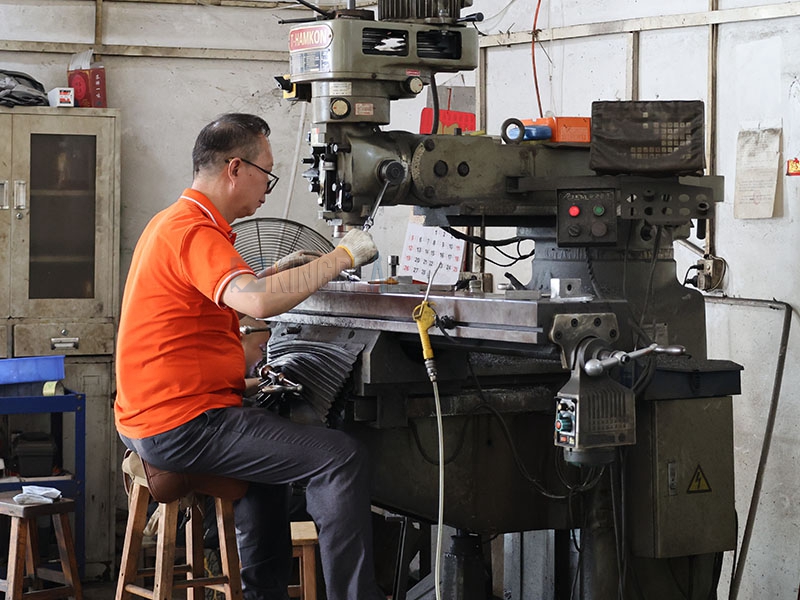
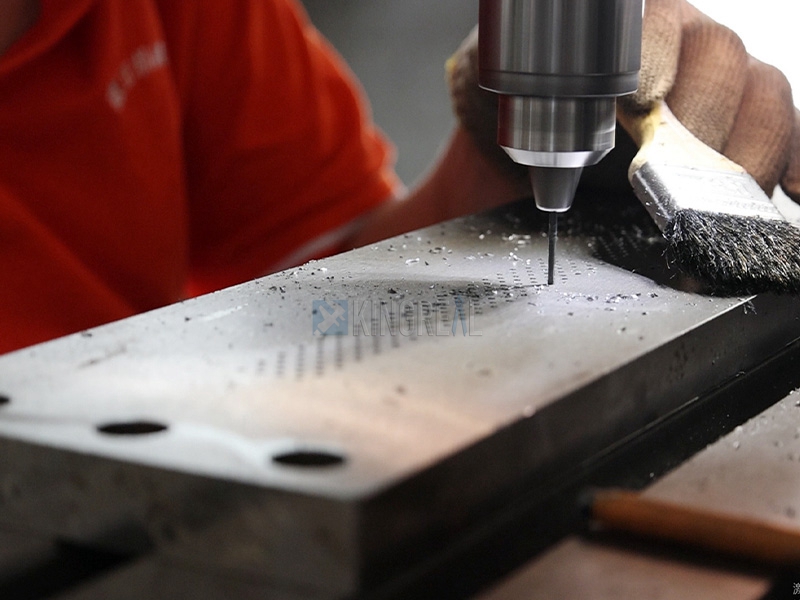
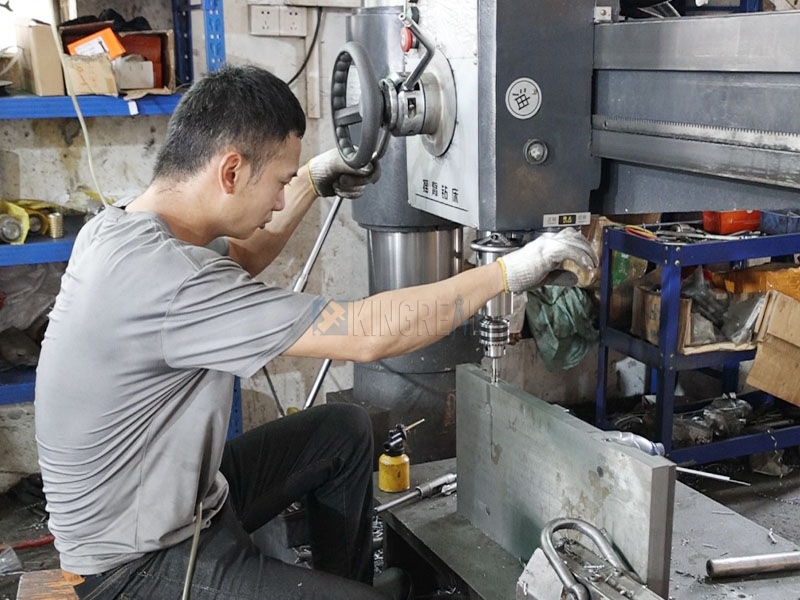
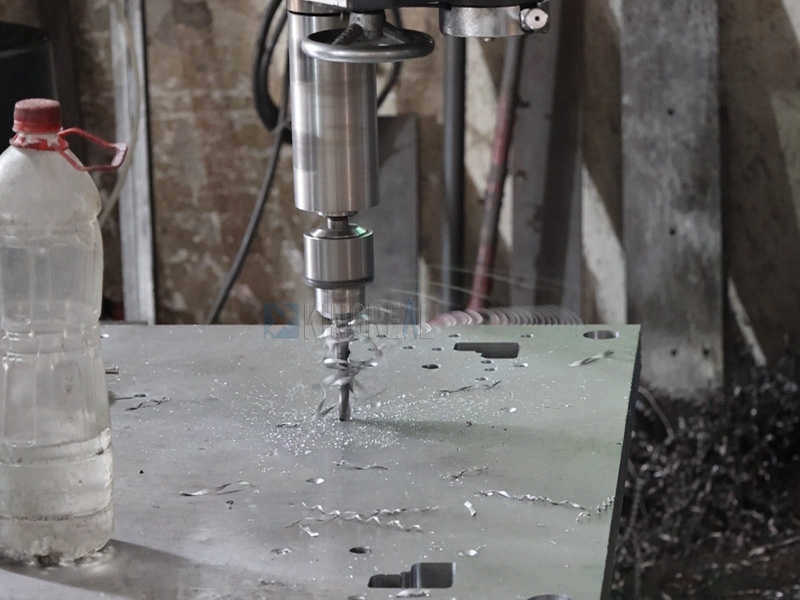
Production details:
The manufacture of punching dies is a crucial part of the metal perforated machine production process. KINGREAL CEILING MACHINERY staff carefully builds each mold to ensure the consistency of each aperture and fully match the customer's drawings. It is worth mentioning that KINGREAL CEILING MACHINERY has significant advantages in the manufacturing technology of micro hole punching dies. The market usually only produces punching dies with apertures of 1.8mm and 2.5mm, while KINGREAL CEILING MACHINERY is able to manufacture punching dies with apertures up to 1.0mm.
This process requires higher manufacturing technology and rich experience. Through continuous technological accumulation and innovation, KINGREAL CEILING MACHINERY ensures the accuracy and reliability of each mold to meet the high standards of customers.
Through the above strict manufacturing process, KINGREAL CEILING MACHINERY can not only ensure the quality of the punching die, but also ensure the efficiency and consistency of the final product, and provide customers with high-quality solutions. KINGREAL CEILING MACHINERY is always committed to technological innovation and quality improvement to meet the diverse needs of the market.
How to ensure the quality of machine processing?
1. Rich manufacturing experience
Experienced team: KINGREAL CEILING MACHINERY staff have rich manufacturing experience, covering all aspects from design to production. Their practical experience enables them to quickly find solutions when faced with complex problems.
2. Rigorous manufacturing process
Full-process monitoring: The factory workshop is equipped with high-definition cameras to monitor the production process in real time to ensure that every step is within the controllable range. Monitoring data can be used for subsequent analysis and improvement.
Inspection team: KINGREAL CEILING MACHINERY has a special inspection team that regularly visits the production site for inspection to ensure that workers operate in accordance with regulations and eliminate idleness and non-compliant behavior. At the same time, the inspection team will also evaluate the production environment to ensure safety and hygiene.
3. Regular spot checks on processed parts
Sampling inspection: During the production process, KINGREAL CEILING MACHINERY will regularly spot check the processed parts to ensure that each batch of products meets the quality standards. These spot checks include dimensional measurement, surface quality inspection, and functional testing.
Data recording and analysis: The results of each spot check will be recorded in detail, and the data analysis team will conduct statistical analysis on the spot check results to identify potential problems and make improvements.
Feedback mechanism: Once a quality problem is found, the relevant department will immediately take measures to rectify it and feedback the results to the production team to prevent similar problems from happening again.
4. Selection of high-quality raw materials
Strict material procurement standards: KINGREAL CEILING MACHINERY sets strict standards for raw material procurement to ensure that the selected materials have high hardness and good durability. All suppliers are subject to strict audits to ensure that their material quality meets international standards.
Material testing: Each batch of raw materials is subject to inspection when entering the warehouse, including physical properties, chemical composition and other related tests to ensure the quality and consistency of the materials.
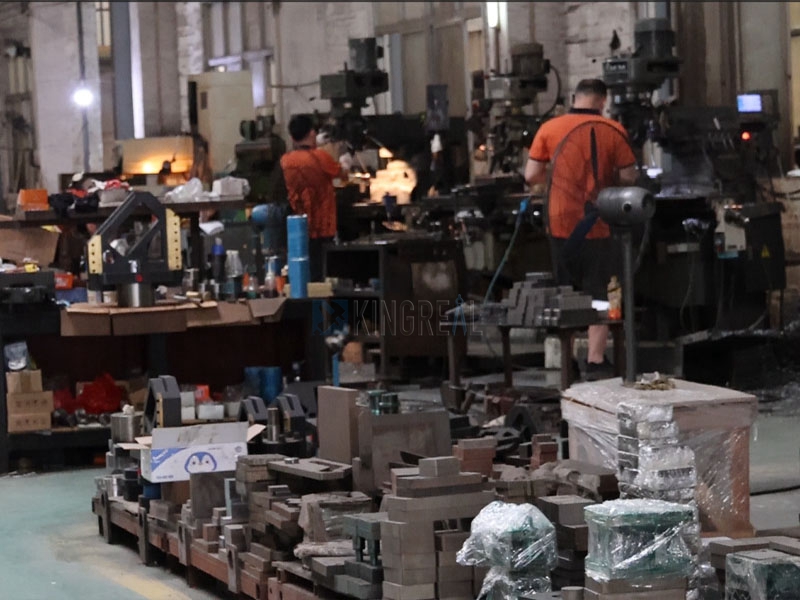
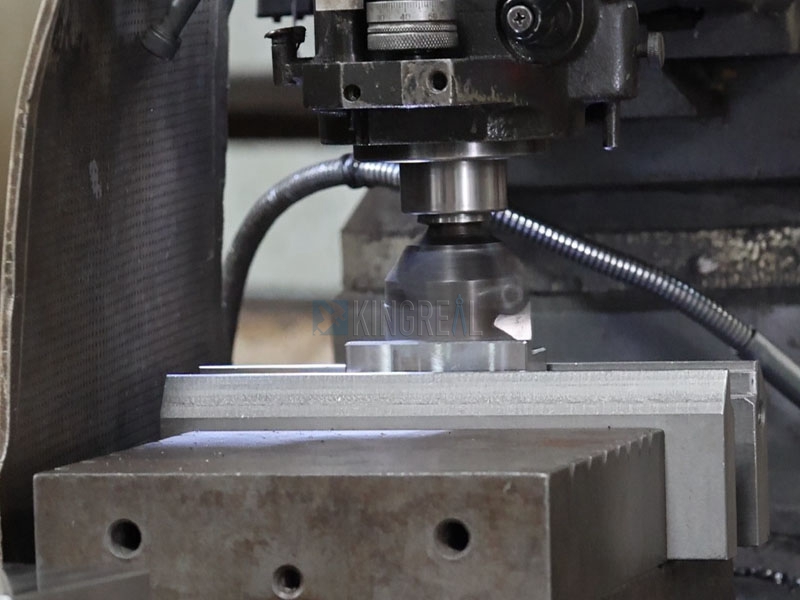
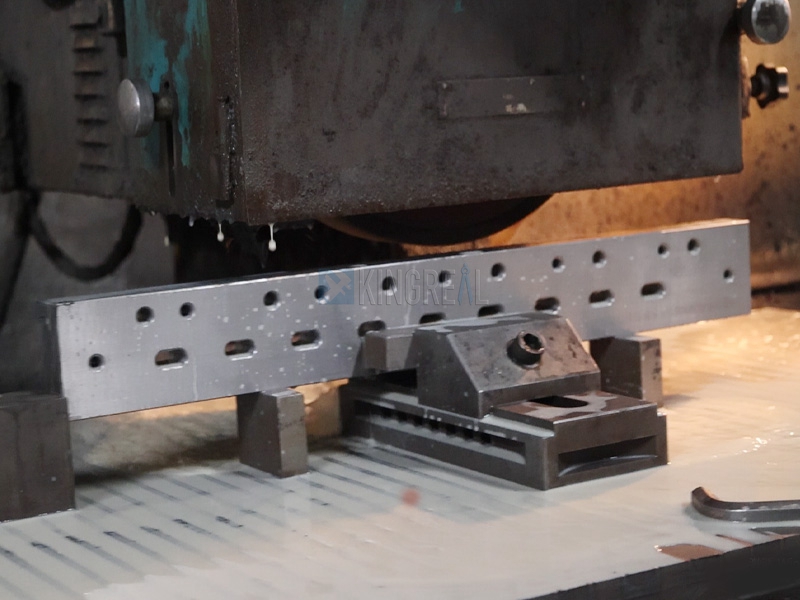
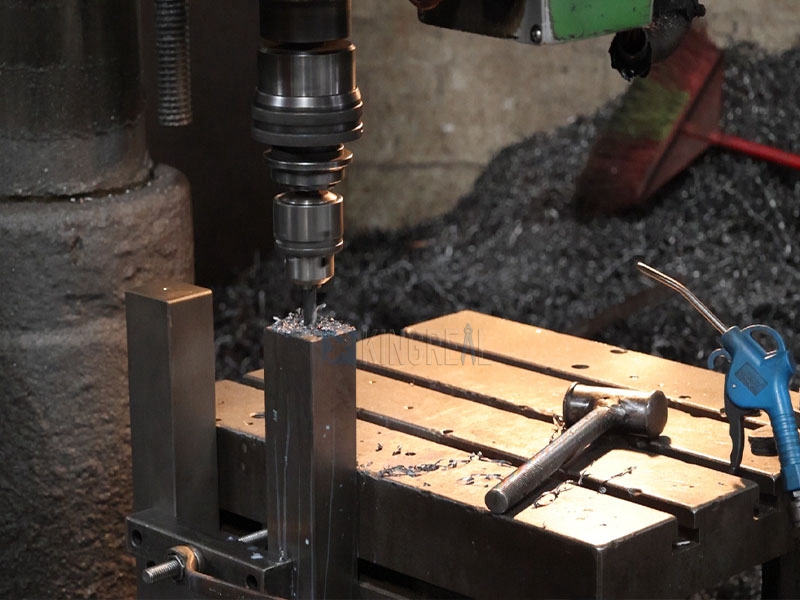
Get the latest price? We'll respond as soon as possible(within 12 hours)