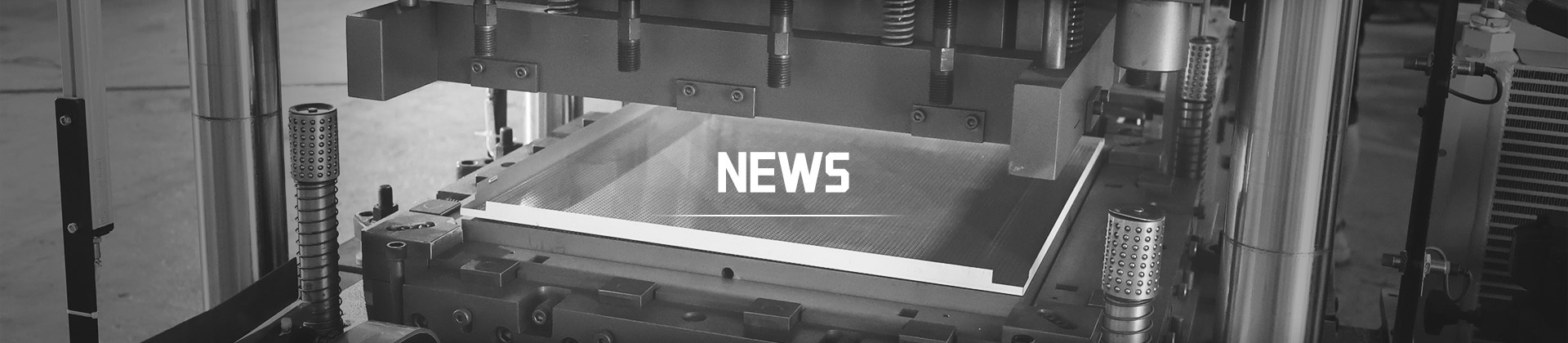
Installation Service--Metal Perforating Machine
2025-01-06 16:28
Video About Metal Sheet Perforated Making Machine
Introduction to the Metal Sheet Perforated Making Machine
The metal perforating machine is an extremely common and important sheet metal processing equipment that can meet the needs of multiple industries for perforated sheets. With its flexibility and efficiency, KINGREAL CEILING MACHINERY sheet metal hole punching machine can handle a variety of raw materials, including aluminum, galvanized steel, stainless steel, etc. This makes it an indispensable part of the sheet metal processing field. | ![]() |
In order to meet the personalized needs of customers, KINGREAL CEILING MACHINERY will adjust the metal perforating machine according to the actual production requirements of customers. For example: - Coil thickness: The equipment parameters can be optimized according to different sheet thicknesses to ensure production efficiency and product quality. - Punching shape: Supports customization of holes of various shapes, including round, square, oval, etc., to meet the needs of different application scenarios. - Production speed: According to the customer's output requirements, adjust the speed level of the sheet metal hole punching machine to achieve efficient production. | ![]() |
KINGREAL CEILING MACHINERY has established long-term cooperative relationships with customers in the fields of construction, electrical and electronic industries, air conditioning and refrigerator manufacturing, machinery and automotive industries, filter production, furniture and lighting industries, etc. with many years of industry experience, providing high-quality metal punching solutions. | ![]() |
Core features of KINGREAL CEILING MACHINERY metal perforating machine
1. Low energy consumption design
KINGREAL CEILING MACHINERY sheet metal hole punching machine adopts advanced energy-saving technology to reduce energy consumption while ensuring that production efficiency is not affected. Compared with most equipment on the market, KINGREAL CEILING MACHINERY's sheet metal hole punching machine can complete the same perforation work with lower energy consumption, saving customers production costs while meeting environmental protection requirements.
2. Easy to operate
KINGREAL CEILING MACHINERY metal perforating machine is equipped with an intelligent control panel with an intuitive and friendly operation interface, which is convenient for operators to quickly get started.
- Touch screen control: Operators can easily adjust parameters such as punching speed, hole shape and cutting length through the touch screen.
- Automation function: reduce manual intervention, reduce error rate and improve production efficiency.
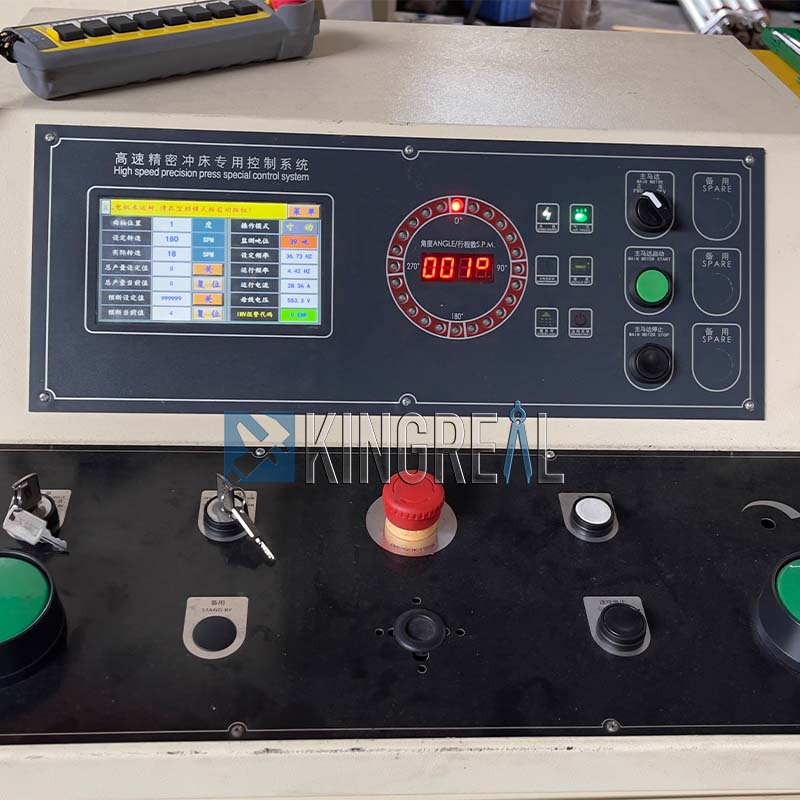
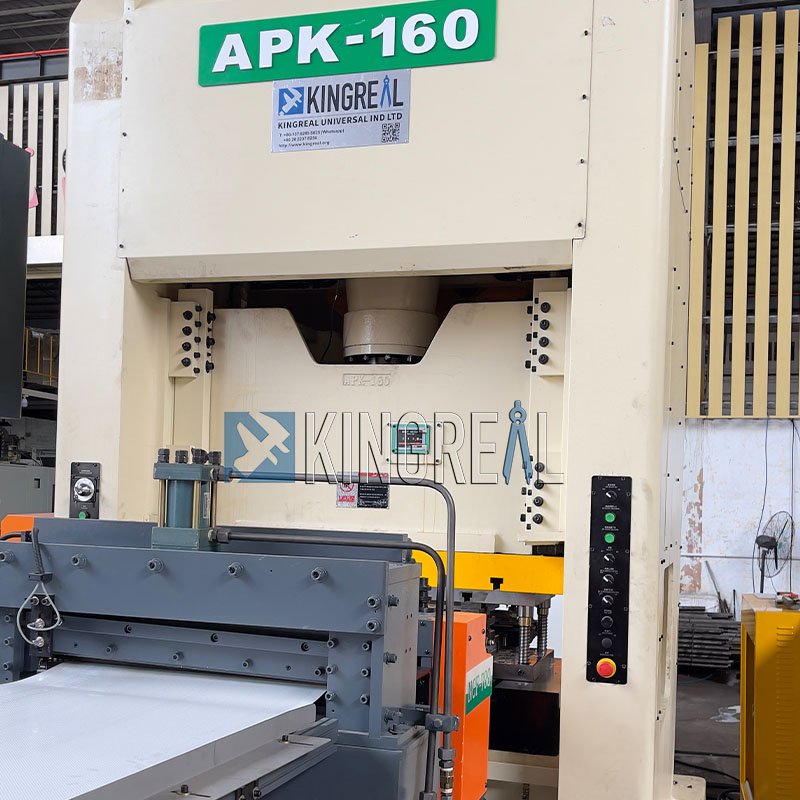
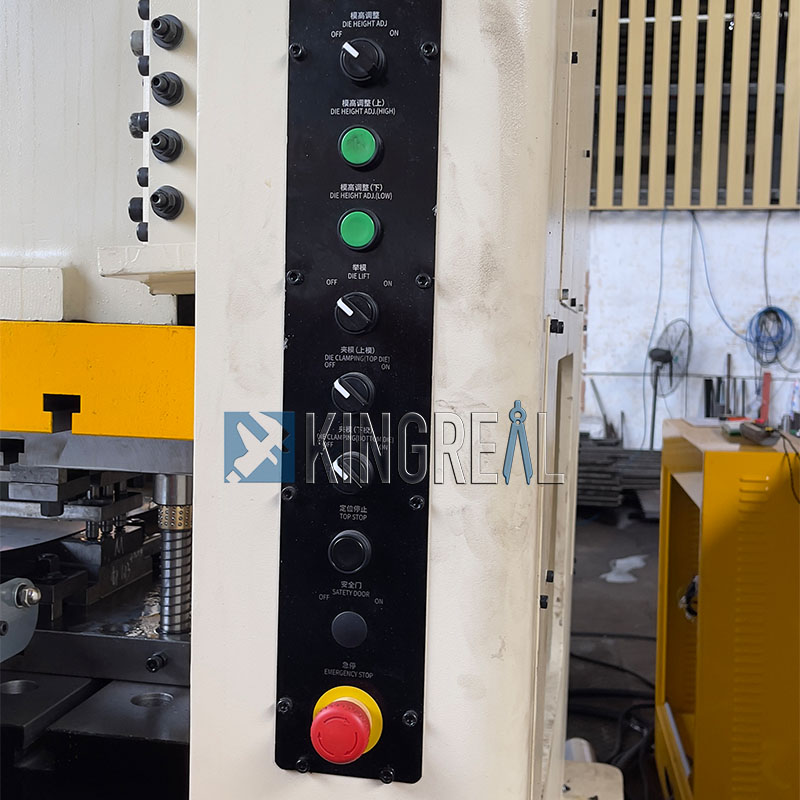
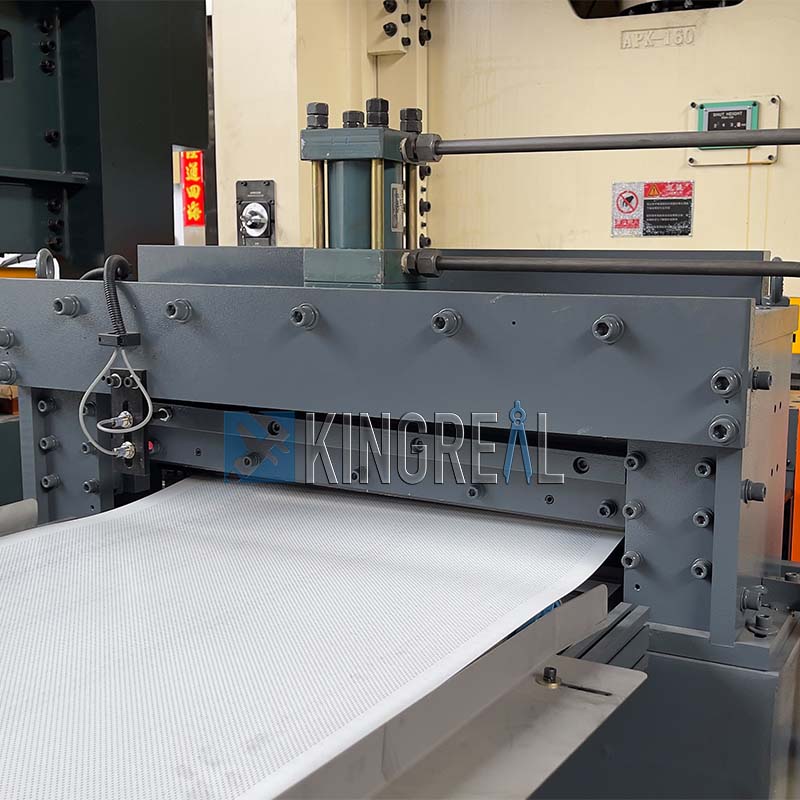
3. Diversified solutions
KINGREAL CEILING MACHINERY can provide metal perforating machine solutions with different speeds and price ranges according to customer needs:
- Speed level: from standard speed to high-speed production to meet different production needs.
- Punching stroke: provide flexible stroke selection to adapt to punching tasks of different sizes and shapes.
- Customized service: customers only need to provide drawings and specific requirements, and KINGREAL CEILING MACHINERY engineers will submit a complete design plan after full communication to ensure that the equipment fully matches the customer's production needs.
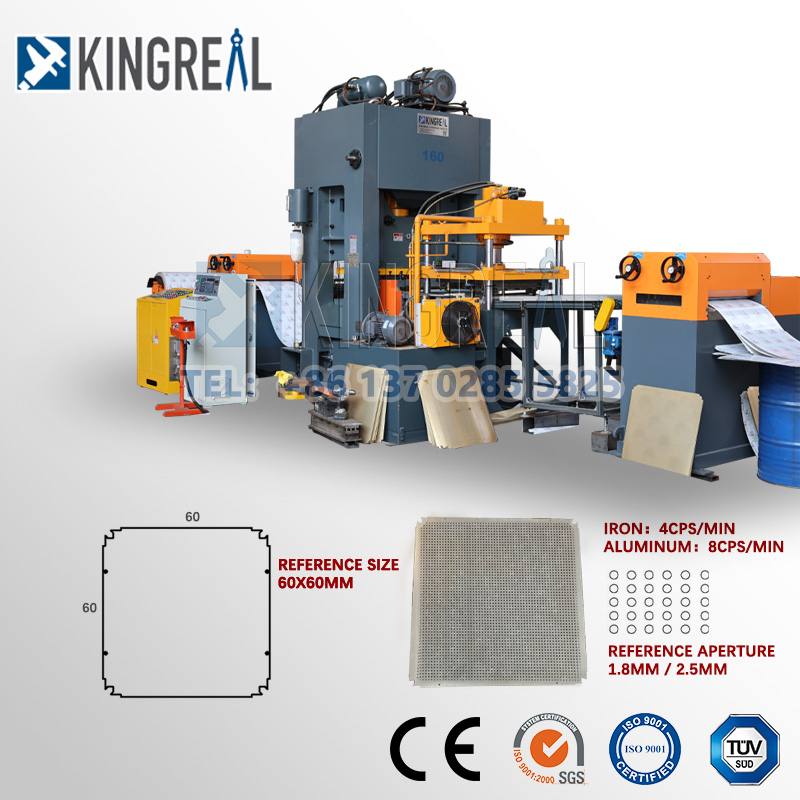
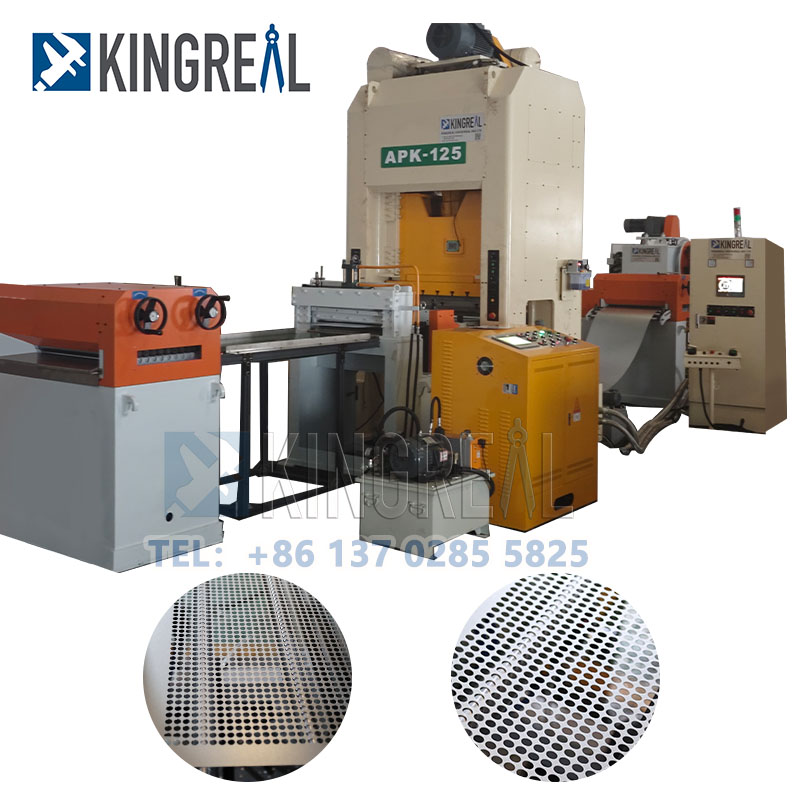
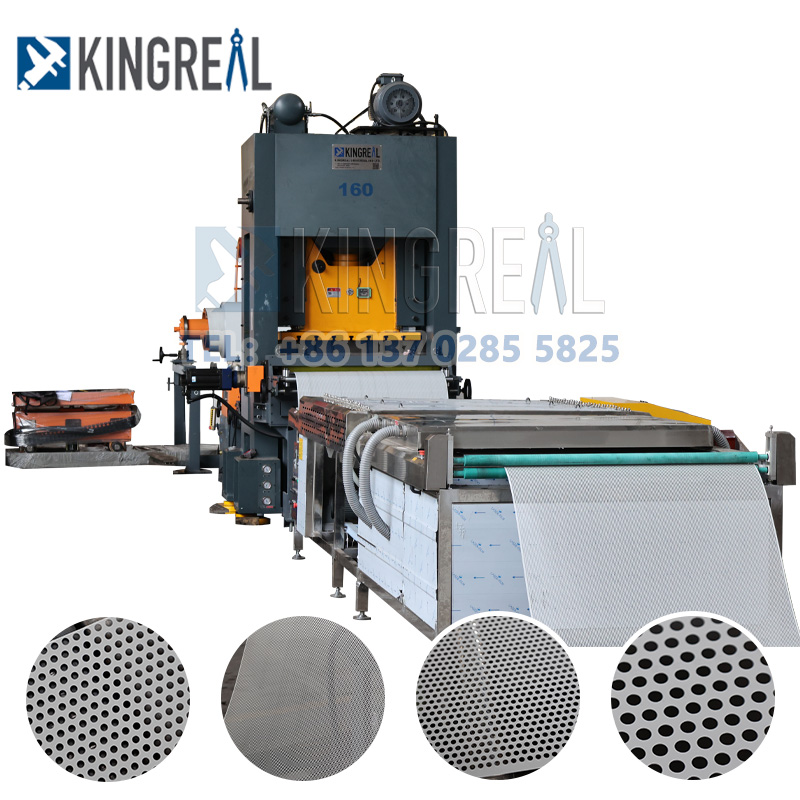
4. Modular design
KINGREAL CEILING MACHINERY sheet metal hole punching machine adopts modular design, which is convenient for equipment upgrade and maintenance. Customers can add functional modules according to future needs, such as automatic stacking device or intelligent detection system, to further improve the efficiency and applicability of the production line.
Installation Service -- KINGREAL CEILING MACHINERY's engineer in Russia
Engineers arrived at the customer's factory
KINGREAL CEILING MACHINERY has always insisted on providing customers with comprehensive service support, including equipment installation, commissioning and operation training. This time, KINGREAL CEILING MACHINERY engineers went to Russia to install a fully automatic metal perforating machine for local customers to ensure that the equipment can be put into use smoothly and meet the production needs of customers.
After the engineer arrived in Russia, he immediately went to the customer's factory and started the intensive installation work.
(1) Equipment acceptance and preliminary inspection
Before the formal installation, KINGREAL CEILING MACHINERY engineers and the customer's team of workers jointly opened the equipment packaging box and conducted a comprehensive inspection of the equipment.
● Component status inspection
The engineer carefully checked the key components such as the decoiler, precision straightener, punching machine, cutting station, etc. to ensure that all equipment was not damaged during long-distance transportation. If any problems are found, the engineer will immediately communicate with the headquarters to arrange replacement or repair.
● Equipment positioning
Use a forklift to transport each component to the predetermined location of the factory. KINGREAL CEILING MACHINERY engineers make precise adjustments based on the layout of the customer's factory to ensure that the equipment layout meets the customer's production process and site conditions.
(2) Equipment assembly and commissioning
After completing the inspection and positioning of the components, the engineer enters the equipment assembly stage. This is the core link in the installation process.
● Equipment assembly
- Engineers assemble modules such as decoiler, precision straightener, punching machine, and cutting station one by one, and connect them into a complete production line.
- During the assembly process, the engineer also introduced the functions and characteristics of each component to the Russian workers in detail, such as the die replacement method of the metal perforating machine and the precision control of the cutting station.
● Test and commissioning
- Test preparation: The engineer puts the metal coil into the decoiler and starts the production line for trial operation.
- Test content:
- Production speed: Test whether the metal perforating machine meets the production efficiency required by the customer.
- Shearing accuracy: Ensure that the machine can accurately shear metal sheets to the specified length according to the input instructions.
- Punching quality: Replace different dies to test whether the metal perforating machine can punch holes of various shapes and sizes on the metal coils, and ensure that the holes are error-free.
- Parameter adjustment: According to the test results, the engineer adjusts the equipment parameters in real time, including punching speed, shearing length, etc., to ensure that the equipment can fully match the customer's production needs.
(3) Operation training
After the commissioning is completed, the engineer began to conduct comprehensive equipment operation training for the workers in the customer's factory.
● Basic operation explanation
- The engineer explained the core operations of the metal perforating machine one by one, including:
- How to change the punching die.
- How to set the metal cutting length of the shearing station.
- How to adjust the punching speed and production parameters.
The engineer uses an easy-to-understand way, combined with actual on-site operations, to help workers quickly master the use of the equipment.
● Practical training
- The engineer invites workers to operate the equipment and guides them beside.
- For improper operation behaviors, engineers will point out and correct them in time to ensure that workers can operate the equipment correctly and safely.
● Answers to key questions
Workers raised some questions during the operation, such as:
- How to quickly change molds to adapt to different production needs?
- How to deal with abnormalities in the equipment?
- How to perform daily maintenance to extend the service life of the equipment?
The engineers answered them one by one and demonstrated the relevant operations to help workers establish a comprehensive operation and maintenance knowledge system.
Get the latest price? We'll respond as soon as possible(within 12 hours)