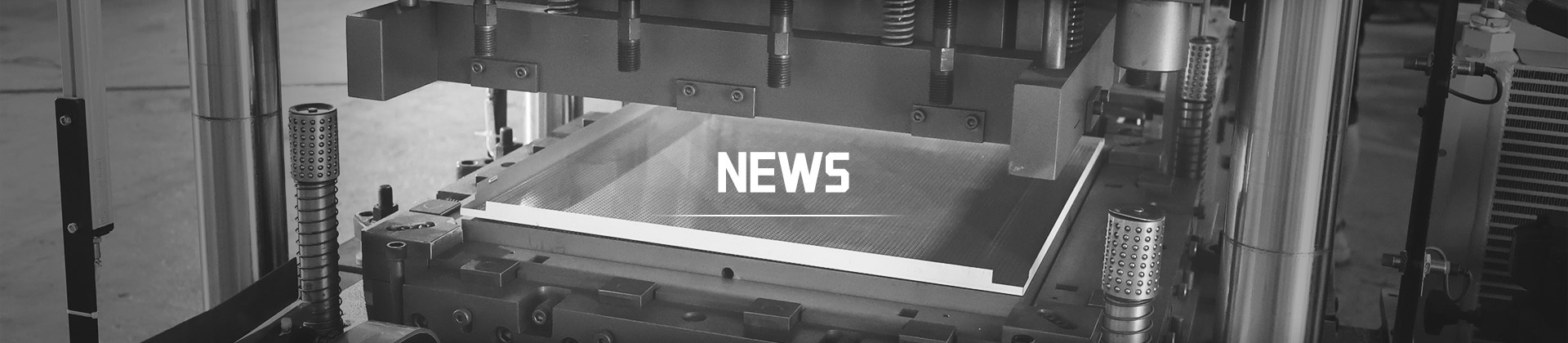
Local After-sales Service -- T Bar Ceiling Machine
2024-11-06 18:29
T Bar Machine Local After-sales Service in Brazil
Recently, KINGREAL CEILING MACHINERY dispatched engineers to Brazil to provide on-site after-sales service for a customer. The primary task of the KINGREAL CEILING MACHINERY engineers was to assemble and calibrate the newly arrived ceiling t bar making machine and train the Brazilian factory workers on its operation.
Upon arriving in Brazil and taking a brief rest, the senior engineers of KINGREAL CEILING MACHINERY quickly headed to the customer’s factory to begin the intensive installation of the equipment.
After-sales Service Process in Detail
First, they meticulously assembled several high-precision machines, including a decoiler, main roll forming machine, punching press, and automatic cutting station, into a complete production line. After assembly, the engineers began trial operations using the raw materials provided by the factory.
During the first trial run, they quickly detected slight discrepancies in the finished product. To ensure product accuracy and quality, they conducted a comprehensive inspection of all t bar ceiling machine parameters and made multiple precise adjustments according to the production requirements.
Following a series of fine-tuning and optimizations, KINGREAL CEILING MACHINERY’s ceiling T bar roll forming machine successfully started operating, producing high-precision finished products that met strict standards, providing the customer with a satisfactory production solution.
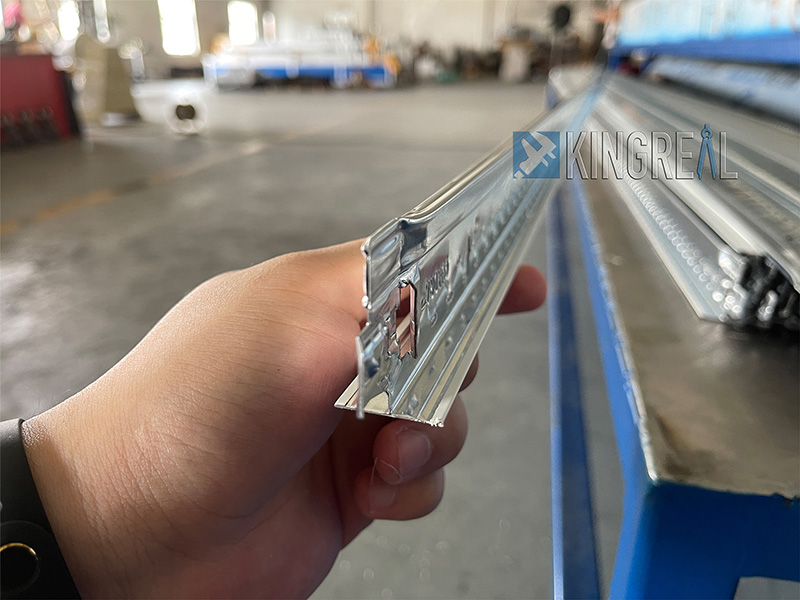
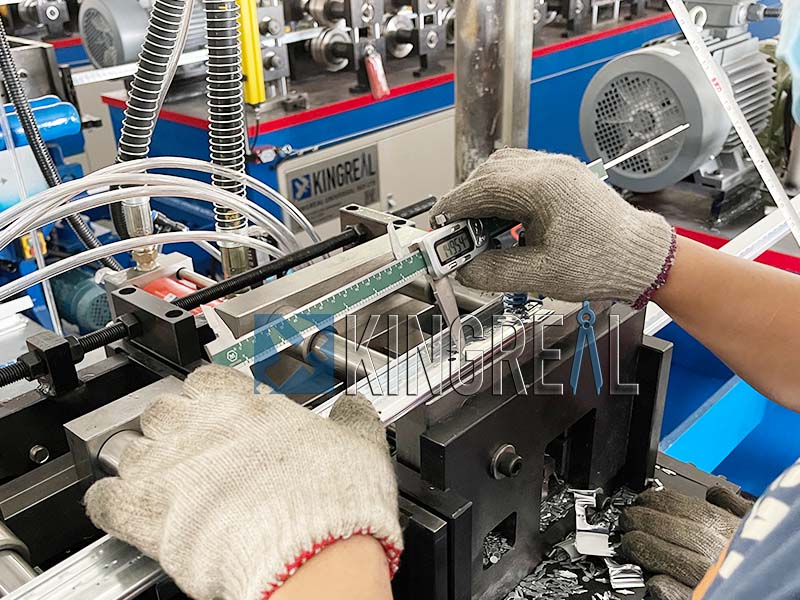
During the ceiling t grid machine’s operation, the factory workers raised many questions, particularly regarding specific operational steps, production efficiency optimization, and safety procedures. KINGREAL CEILING MACHINERY’s engineers patiently answered each question and demonstrated the operation, combining theory with practice. The workers were especially curious about how to produce different-sized products using the same t bar ceiling production line. In response, the engineers explained in detail that producing different sizes mainly involves changing the roller sets and cutting molds.
To make the process more intuitive, the engineers not only gave detailed verbal explanations of each step but also personally operated the equipment, showcasing the entire process from changing the roller sets to adjusting the cutting molds. This approach deepened the workers’ understanding and enhanced their confidence and skills in operating the equipment. After fully training the Brazilian factory workers, KINGREAL CEILING MACHINERY’s engineers stayed on-site for a while, closely monitoring each production step to ensure the workers could proficiently operate the ceiling t grid machine and that the finished products met strict quality standards.
This visit by KINGREAL CEILING MACHINERY engineers to the Brazilian factory for on-site after-sales service not only demonstrated their exceptional technical capabilities but also underscored the company’s high regard for product precision and customer needs.
Video About Ceiling T Bar Machine
KINGREAL CEILING MACHINERY's Service
KINGREAL CEILING MACHINERY has always placed a strong emphasis on service. Whether it’s pre-sales, during sales, or after-sales, KINGREAL CEILING MACHINERY is committed to providing customers with professional and comprehensive service. KINGREAL CEILING MACHINERY has established a complete after-sales system, ensuring that KINGREAL CEILING MACHINERY’s customers have no concerns about post-purchase issues.
Whether it’s machine installation, worker training, or troubleshooting, KINGREAL CEILING MACHINERY’s engineers are available to provide timely and professional on-site service. If you encounter any issues while using the T bar ceiling roll forming machine, the KINGREAL CEILING MACHINERY technical team offers 24/7 online support. Your satisfaction is always KINGREAL CEILING MACHINERY’s top priority!
Get the latest price? We'll respond as soon as possible(within 12 hours)