4 High Roller Leveling Machine
The KINGREAL 4 High Roller Leveling Machine is one of the most emblematic leveling machines, offering convenience, economy and precision within the leveling range. 4 The High Roller Leveling Machine is capable of leveling different types of products, including sheet metal and perforated metal products.
- KINGREAL CEILING MACHINERY
- CHINA
- 90 DAYS
- 9999
Details
Video About Plate Leveller Machine
Description Of 4 High Roller Leveling Machine
4 High Roller Leveling Machine is a kind of industrial equipment used to process plates, usually used to level or straighten metal plates to reduce the warping, waving, bending, and other surface unevenness of the material.
KINGREAL CEILING MACHINERY 4 High Roller Leveling Machine usually uses four rolls to process the metal material so as to ensure its surface flatness. The specific structure consists of two sets of work rollers, usually one set is located above and the other below, and the sheet metal is leveled by pressure between the upper and lower rollers.
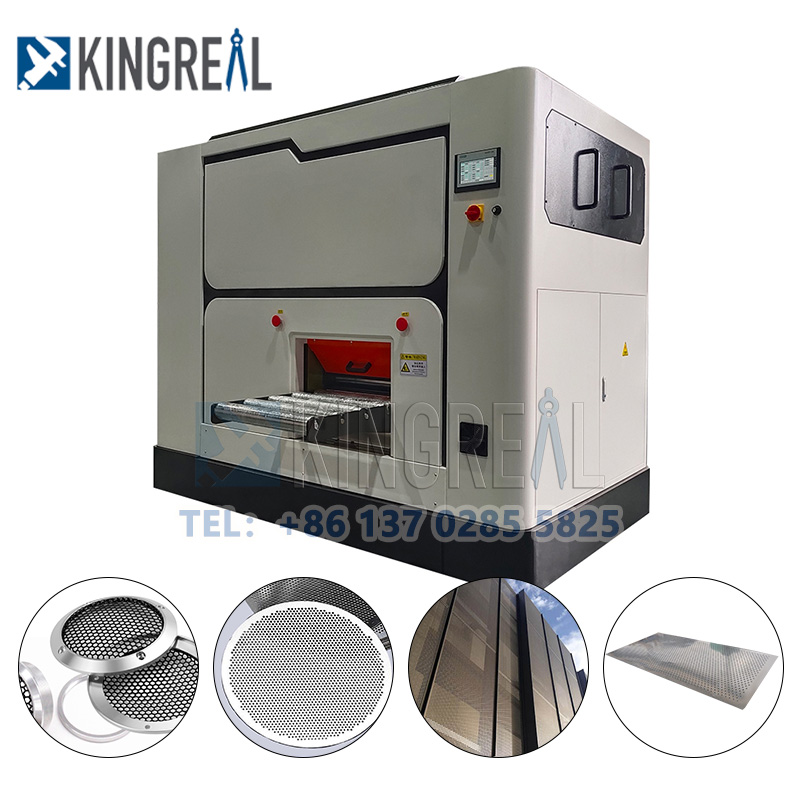
Principle Of Four High Leveling Machine For Metal Sheet
1. Basic structure
Four working rolls: The four heavy leveler mainly consists of two support rolls on the top and bottom and two leveling rolls on the top and bottom. There is a pair of rolls on the top and a pair of rolls on the bottom. The plate passes between the four rolls and is controlled by the pressure and gap between the rolls for leveling.
Upper work roll: Located above the plate, it is responsible for applying pressure to the upper surface of the plate.
Lower work roll: Located below the plate, it supports and levels the lower surface of the plate.
Supporting roller: to prevent the working roller from deformation during the process and to improve the leveling accuracy.
2. Working Principle
The working principle of the four-weight leveling machine is based on the force state of the metal sheet between the rolls. By adjusting the gap and pressure between the four working rolls, the plate passing through is subjected to different degrees of bending and reverse bending, and finally the flatness of the material surface is realized.
3. Key working principle steps:
Feeding: the metal sheet to be leveled enters the leveler from the feeding end.
Initial bending: When the metal sheet passes through the upper and lower working rollers, it will produce initial bending deformation. Depending on the thickness and material of the sheet, the leveler can apply appropriate pressure, causing controlled plastic deformation of the sheet surface.
Reverse bending: As the sheet passes between the four rolls, the direction of force will change. The lower work roll will reverse correct the plate after bending. This process is repeated several times to remove stress and warpage from the sheet.
Multiple Leveling: Through many repeated bending and releasing, the irregular deformation of the plate such as wave and bend is gradually corrected and the surface tends to be flat.
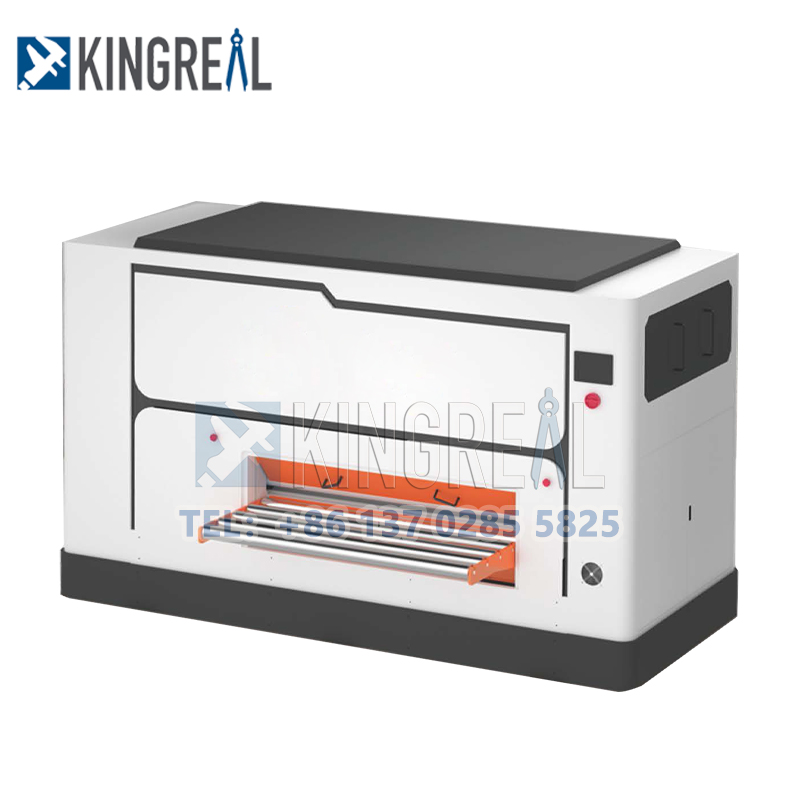
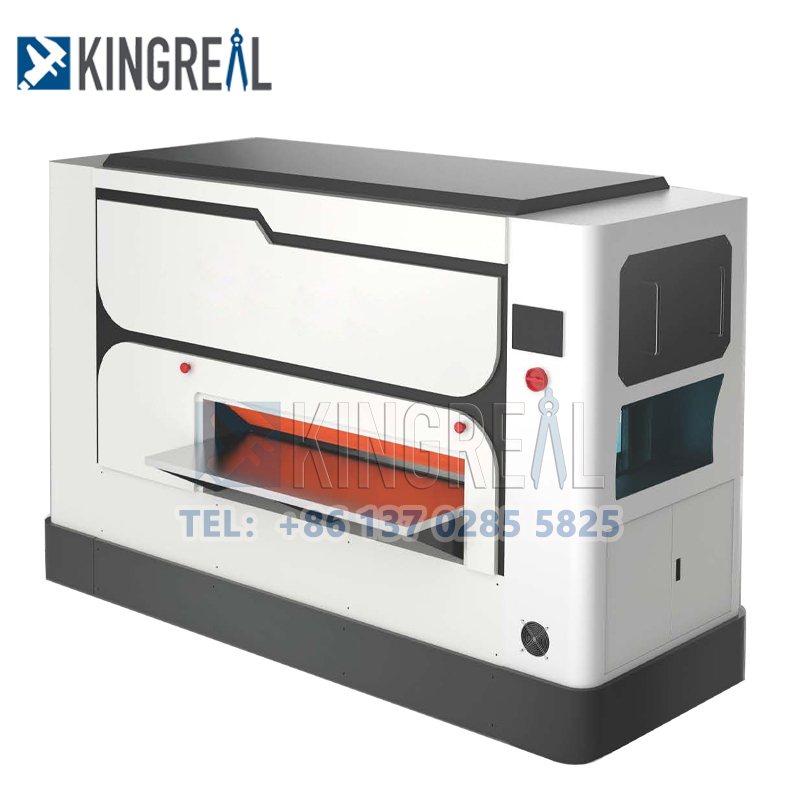
Unique Design Introduction-- Leveling Roller Box Convey Out Device
The support rollers and leveling rollers bearings are mounted on a movable plate. After the upper leveling roller frame was electrically lifted, the movable plate will be driven out by the motor. Then after removing the bearing front the baffle, the roller can be taken our from the fixed rear bearing, so it’s convenient and save much time to clear leveling rollers, support rollers, support plated etc.
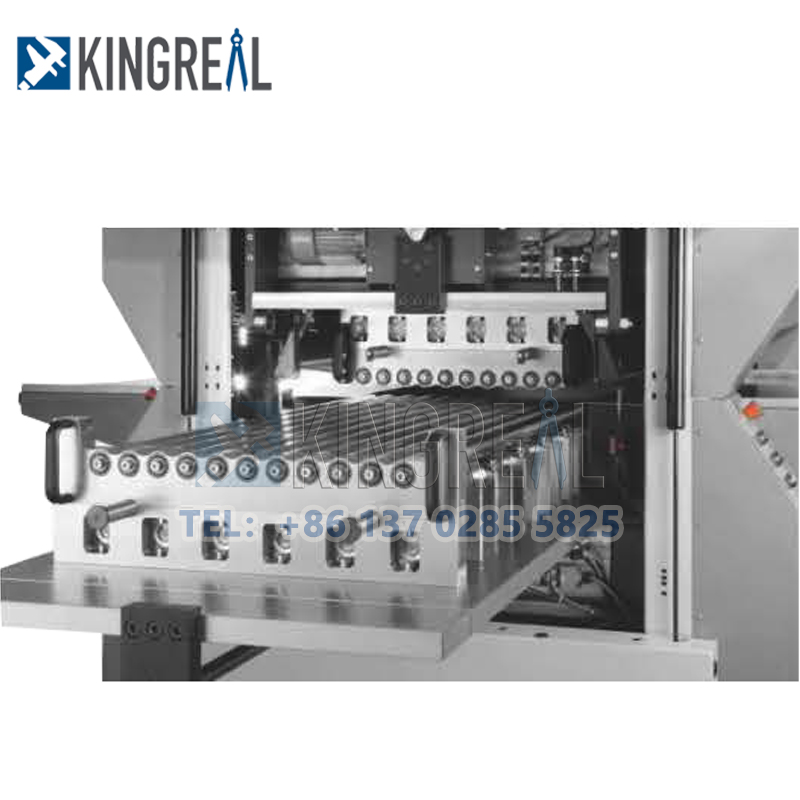
Technical Specification
Max. Criterion Width | 1200-1300MM |
Roller Diameter | 20MM |
Max. Thickness | 1.5MM |
Thickness Range | 0.2-1.5MM |
Min. Work Piece Size | 10*40MM |
Leveling Speed | 0-12M/Min |
Parameters to be determined before obtaining a quote:
√Materials for leveling
√Thickness of the leveling
√The shape of the leveled product
√Dimensions of the leveled product (length, width)
Product Display
In the manufacturing process, KINGREAL CEILING MACHINERY's metal plate leveling machines use high-quality raw materials with high hardness and strength to make roller wheels. These high-quality rollers not only have excellent wear resistance and deformation resistance, but also can withstand high working pressure, thus ensuring excellent performance in the leveling process.
The precise fit of the upper and lower rollers allows the sheet metal to be stretched and compressed repeatedly. This process effectively releases the stress inside the material, making the leveling effect of the plate significantly improved.
In addition, the roller design of the KINGREAL CEILING MACHINERY plate leveller machine is carefully optimized to ensure an even distribution of pressure, further enhancing the levelling effect. Such a high standard manufacturing process not only improves the performance of the metal plate leveling machine, but also provides customers with more reliable leveling solutions, helping all kinds of metal processing enterprises to achieve higher production efficiency and product quality.
Product Tag
Get the latest price? We'll respond as soon as possible(within 12 hours)